Process
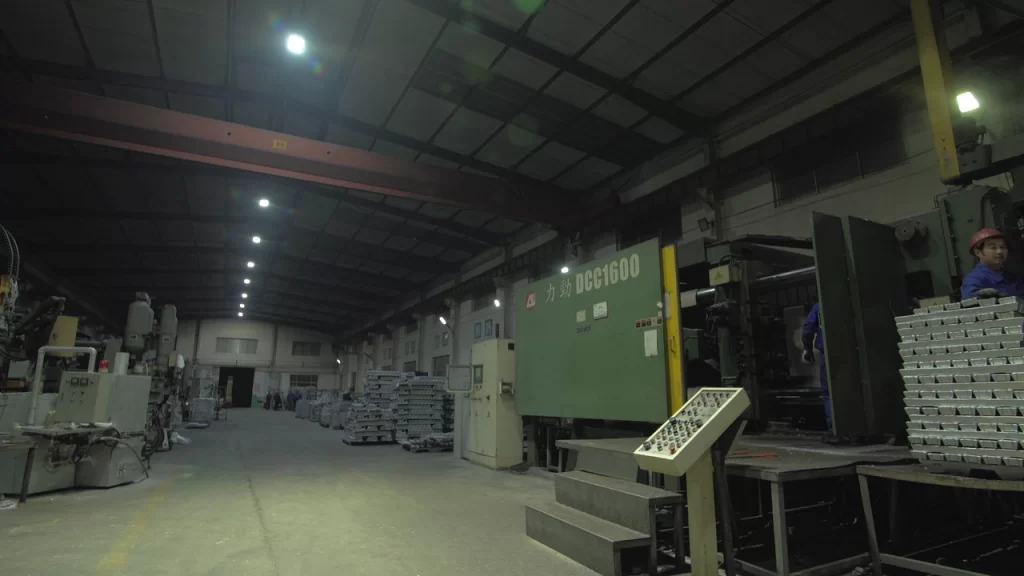
Die Casting
Die casting is the process where molten metal is injected into a mold under high pressure in the range of 10 to 210 Mpa. This will result in a highly uniform casting with very good surface finish and exceptional dimensional accuracy. Usually this can either eliminate or greatly reduce the machining required to finish the part. We could offer both the cold chamber process and the hot chamber process. In the cold chamber process the metal is ladled into the injection chamber for each shot. This is less exposure of the molten metal to the chamber walls and plunger. This is very useful for aluminum and cooper alloys that would easily alloy with iron at elevated temperatures. The hot chamber process has the injection chamber which is connected to the die cavity permanently immersed in the molten metal. The hot chamber process is used for metals of low melting point and high fluidity such as tin and zinc. Minimum wall thickness and draft angles for the die castings are as follows:
The material that MF offers are alloys of aluminum, copper, zinc and magnesium. Zinc castings can be made with thinner wall thickness than aluminum due to high melt fluidity. MF could produce parts from very small to about 30Kg for aluminum, 10Kg for magnesium, 50Kg for zinc and 5Kg for copper.
Aluminum Extrusion
In fact, we rarely supply aluminum profiles directly to customers. Most of the aluminum profile products we produce have undergone deep processing, such as stamping, punching, anodizing, spraying and so on.
The products are also widely used, some are used in the cabinet doors of the Nordic kitchen cabinets, some are used in the drawer handles of the file cabinets, some are used in the display light bars in the American gun cabinets, and some are used in the Australian off-road vehicles. on the roof rack.
What metals are forged?
Just about any metal can be forged. However, some of the most common metals include: carbon, alloy and stainless steels; very hard tool steels; aluminum; titanium; brass and copper; and high-temperature alloys which contain cobalt, nickel or molybdenum. Each metal has distinct strength or weight characteristics that best apply to specific parts as determined by the customer.
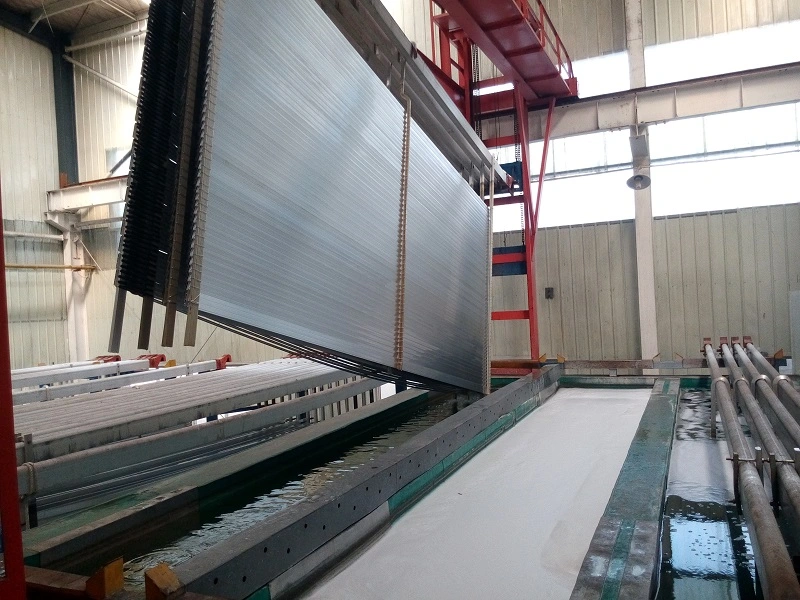
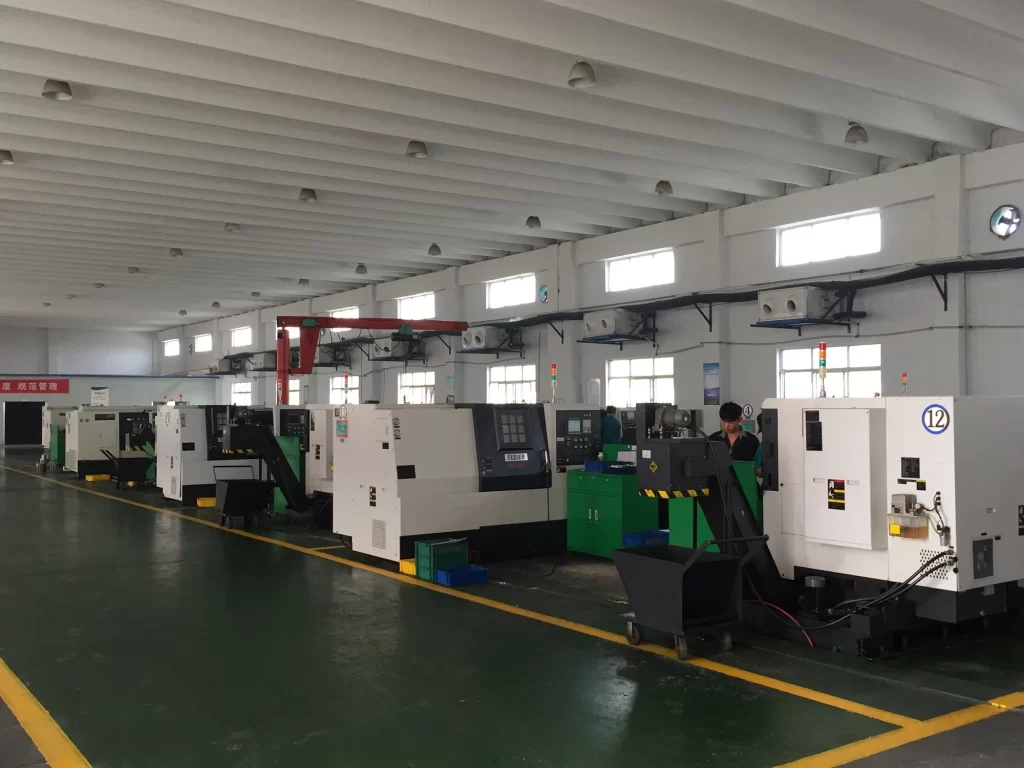
CNC Machining
Perhaps the metal cutting process is what we are most familiar with and good at. Because most of the products require post-processing processes such as turning external circles, internal holes, drilling, tapping, and milling planes, so if you have been operating in our industry for a long time, you will be involved in metal cutting. Equipment, cutters, guages, jigs, inspections, etc. will be well understood, and we as professionals are no exception!
We can provide any metal cutting method: turning, milling, planing, grinding, wire cutting, laser cutting, EDM
We can give you advanced equipment support: 3-axis three-link high-speed milling machine, 4-axis three-link CNC machining center, five-axis five-link precision machining center
According to your product, we will formulate the most cost-effective machining solution for you!
Investment Casting
MF have two types of investment casting processes: silica sol process and the water glass process.
The silica sol process is used to cast complex high quality parts with requirements of a very good surface finish and close dimensional tolerances.
The water glass process is typical of the process in the early stages of investment castings. It generally is capable of much larger castings than the silica sol process, but does not have as good of surface finish or tolerances. The water glass process provides parts that have better surface finish and dimensional tolerances than sand castings.
Silica sol investment castings can range from a weight of just a few ounces to approximately 80 pounds. If you are concerned with precision in very small parts, we are especially proficient at very fine detail work including teeth and serrations. Water glass castings may range in weight from several ounces to approximately 200 pounds.
First article layouts and spectrometer material certifications are provided with all first article samples.
A variety of secondary operations can be performed on both types of investment castings. They include heat treatment, machining, plating, painting, polishing and buffing, assembly services and even custom packaging.
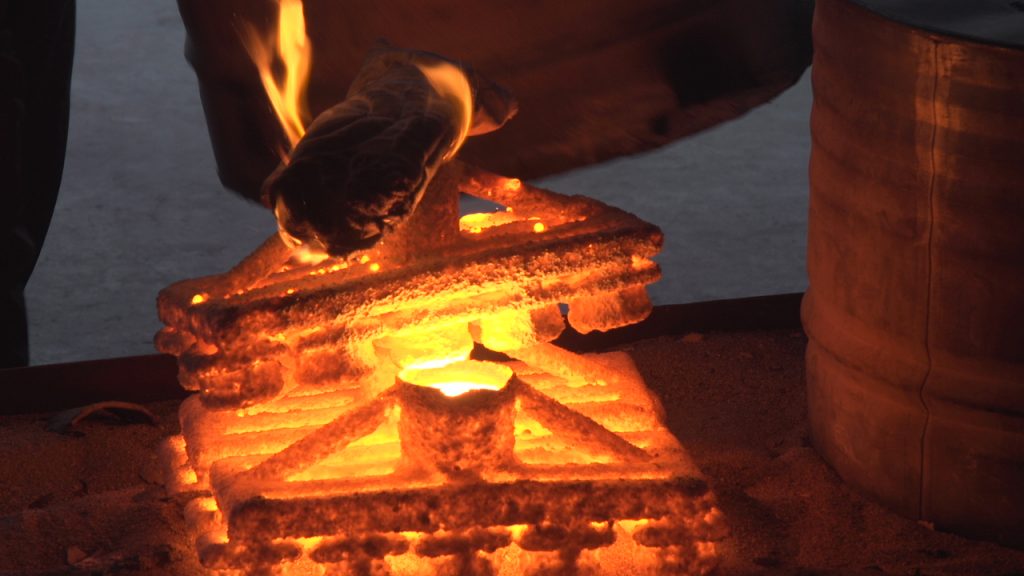
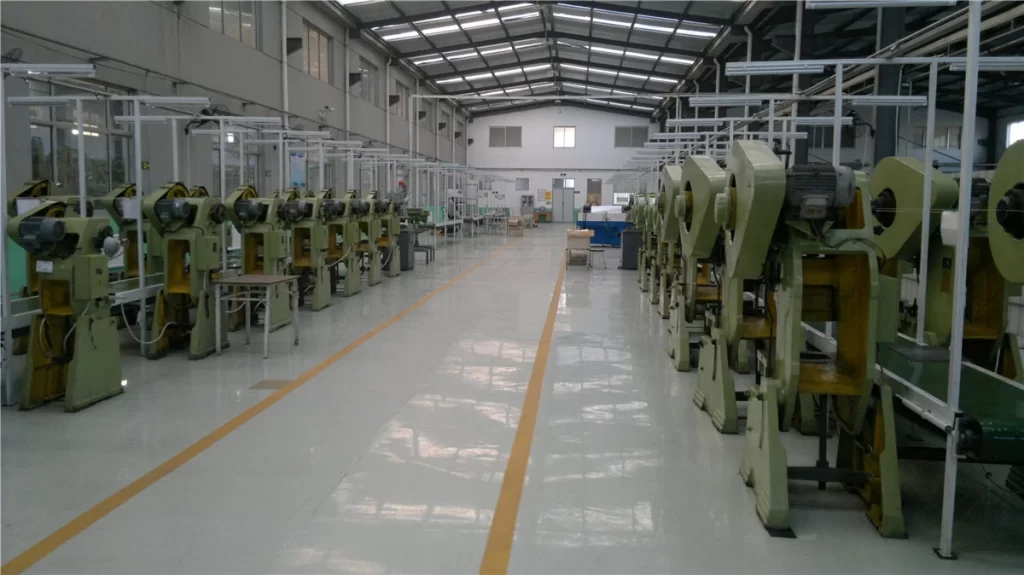
Punching and Deep Drawing
Thanks to the support of Samsung, LG and other customers, we provided them with a large number of precision stamping products in the early stage, so our stamping production line is growing in scale and our workers are becoming more and more skilled.
We now have more than 100 small punching machines, which can be flexibly combined into production lines according to the needs of the order. With the conveyor belt, the daily production capacity can reach tens of thousands of pieces.
Hot Forging
7 forging lines with the capacity of 2000ton,1000 ton, 630 ton, and 400 ton and 200 ton and 100 ton respectively. With own heat treatment lines, MF also embraces many CNC machining equipment, products surface oxide lines and a series of supporting professional testing equipment in order to satisfy customers’ requirements.
What metals are forged?
Just about any metal can be forged. However, some of the most common metals include: carbon, alloy and stainless steels; very hard tool steels; aluminum; titanium; brass and copper; and high-temperature alloys which contain cobalt, nickel or molybdenum. Each metal has distinct strength or weight characteristics that best apply to specific parts as determined by the customer.
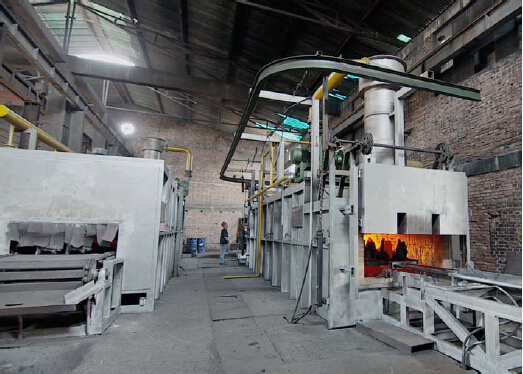
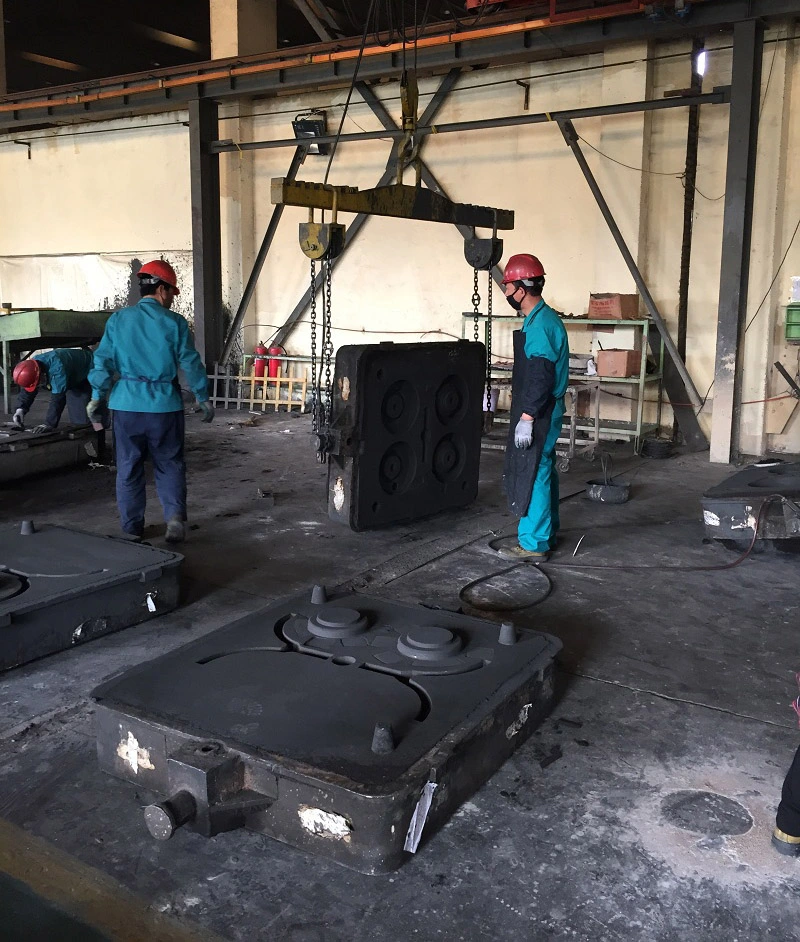
Sand Casting
Sand casting is perhaps the oldest and most commonly used type of metal forming in the marketplace today. It is capable of forming both large and small parts and can be used for a number of different materials.
We have green sand castings, resin sand casings and water glass sand castings in both ferrous and non-ferrous materials.
Perhaps the most common green sand castings would be made from either grey iron or ductile iron. We can supply these castings from approximately 0.05Kg to approximately 15000 Kg and up to 5000mm x 2000mm x 1500mm in size for the largest part. Molding methods range from floor hand molding, jolt squeezer lines and automatic molding lines. With this variety of molding methods we are able to accommodate the weight, size and quantity the customer requires.
Steel sand castings are available both as water glass sand castings and resin sand castings, and are available in plain carbon, alloy and stainless steels. In the category of steel sand castings the smallest available part would be approximately 1Kg while the largest would be approximately 20 tons. Steel castings smaller than the 1Kg range would be made from investment casting(lost wax casting) method.
Non-ferrous sand castings are also available. The molding process used is green sand and we can accommodate requests for castings weighing from 0.1 Kg to 100 Kg. The alloys that are available include copper base and aluminum base alloys.
First article layouts and spectrometer material certifications are provided with all first article samples. Specialized inspection reports can be done per customer request.
A variety of secondary operations can be performed on all three types of sand castings. They include shot blasting, heat treatment, machining, surface treatment, assembly services and even custom packaging.